On bulbs (and keels)
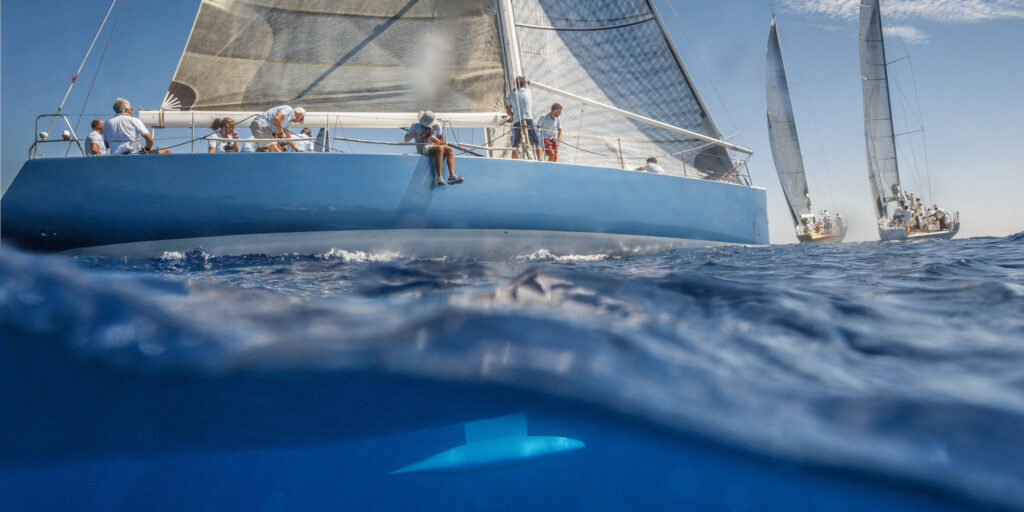
Bulbs are ballasted, non-lifting bodies attached to the tip of keels that are used to improve the boat’s stability. Modern racing rules based on velocity prediction programs do not penalize stability as much as the older ones did. As a consequence, more and more boats are equipped with bulbs today.