Common mistakes in Maxsurf Modeler projects
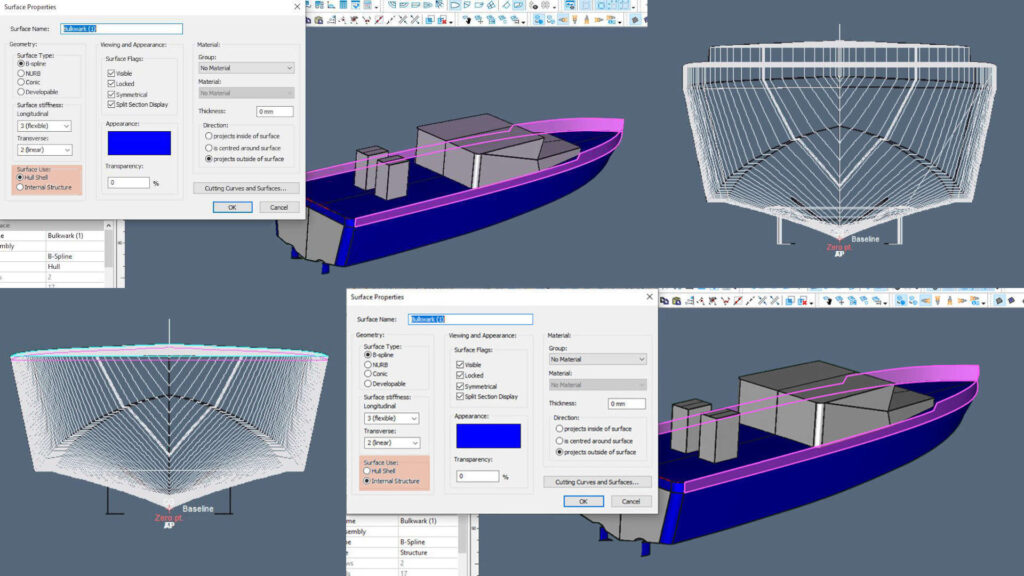
Maxsurf Modeler users often try to create a model that closely resembles the real boat. That is, as if it were a rendering intended to promote the project, including all kinds of details, both internal and external. This idea is common among students and professionals in the area.